5. Transfer roller
The role of the transfer roller is mainly to transfer the paper between the color groups. For single-sided multi-color printing, the middle transfer cylinder must be an odd number so that the printing surface is always guaranteed to be facing upwards on the impression cylinder, as shown in Figure 3.24.
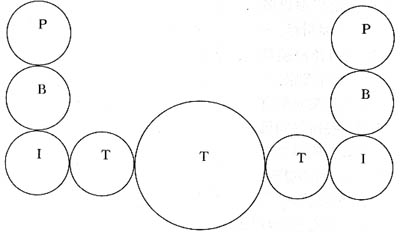
According to the size of the printing web and the size of the operating space, the number of transfer cylinders is selected. For the four start-ups, a large double-diameter transfer drum can be used between the two units, because its web size is small and can be operated simultaneously on both sides. If three rollers are placed in the middle, the space occupied is large and there is no greater practical significance. Instead, the overlay accuracy is affected. For the three transfer rollers available in the middle of the boot, because the open version is relatively large, it is inconvenient to operate on both sides and needs to be operated in the middle of the two groups.
At present, there are also full double-diameter cylinders on the paper transport path for the start-up, as shown in Figure 3.24b.
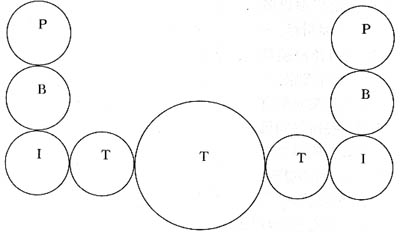
The middle transfer drum becomes one. The instant that the impression cylinder conveys the paper to the transfer cylinder, may not be completed for large-scale paper printing, so that the transfer cylinder also actually plays the role of printing, so the requirement for this cylinder bite is exactly the same as that of the impression cylinder. One of the requirements for this roller is to prevent the back of the paper from picking up, because the printing surface is stuck on the surface of the roller, but the ideal solution should be solved from the design, that is, after the printing on the platen roller is completed, pass the paper to the transfer. roller.
6. Movement of paper in the printing unit
The movement of the paper on the impression cylinder has been analyzed in detail, and the movement of the paper on the other cylinder is exactly the same as that of the impression cylinder, that is, the paper must always be in a controlled state (positioning retentivity) in the printing unit. The key to the movement of the paper in the drum is the movement during mutual exchange, as shown in Figure 3.25 and Figure 3.26.
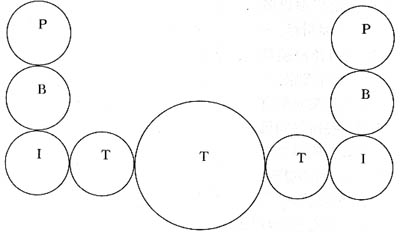
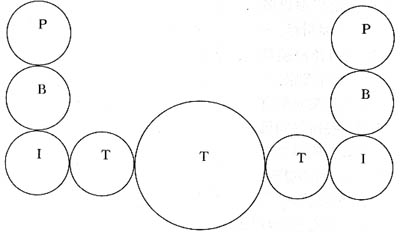
(1) The first stage of the transfer The first group of teeth bite the paper, while the second group of teeth has just opened, and the pads and the teeth are on the top and bottom of the paper.
(2) The second phase of the handover The first group of teeth still bite the paper, and the second group of teeth bite the paper.
(3) The third stage of the exchange At this point, the first group of teeth opened and the second group of teeth continued to bite the paper, thus completing the paper transfer.
The transfer of the paper should be done on the premise that the tooth pads are parallel, so the gap between the two sets of tooth pads has a significant influence on the transfer of paper. In terms of printing requirements, the front opening of the paper should always be kept in a horizontal plane, but this is difficult to do during the handover process, as shown in Figure 3.27.
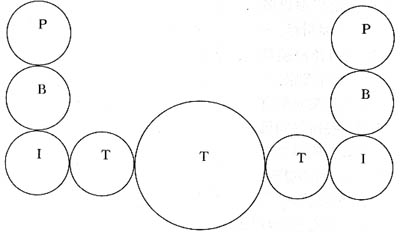
As can be seen from the figure, there is only one type of paper that is just suitable, ie, biting teeth to bite the paper, and its thickness is equal to the distance between the two groups of tooth pads. When the paper thickness difference is too great, the undulation of the paper front mouth becomes more prominent, so each machine has its own suitable paper thickness range. To check the working condition of the teether, observe with the thinnest paper full-size version given in its technical condition.
In terms of printing requirements, the paper should always be kept in close contact with the drum, ie it is surrounded on the surface of the drum. However, because the thickness of the paper is not the same, the thinner the paper, the better its flexibility, the smaller the tendency of tangential orientation, the easier it is to adhere to the surface of the drum; the thicker the paper is, the worse the flexibility is, the stronger the tangential orientation is, The less adhered to the surface of the roller, it may collide with other contact surfaces, so that the surface of the printed product is dirty.
Therefore, the thicker the paper, the larger the diameter of the drum, but the increase in the diameter of the drum is limited, and it is impossible to make it like a platform. In order to keep the paper from colliding with other parts, a suction device is provided inside the drum to suck the tail of the paper, and a blowing device is installed outside the drum to press the paper against the surface of the drum.
7. Open and close teeth cam
When the teeth of the drum are exchanged, they must be opened and closed by a special mechanism. This special mechanism is to open and close the dental cam. There are two kinds of open and close teeth cams: one is high-point closed teeth, and the other is low-point open teeth; the other is low-point open teeth and high-point closed teeth. The high point of closure is the use of a forced cam to close the bite, which is stable and reliable. At the low point, the teeth are opened by the restoring force of the spring. The low point of closing the teeth is using springs to close the teeth at low points. When the machine is low speed, and the real ground is not large, this way of opening and closing teeth can also be. When the speed is high, the printed solid surface is enlarged, and the spring may not be stable due to its own habits, and at this time, the force of the spring is minimal, and it is easy to cause the paper to slide. When open teeth forced open by cam. From a mechanics point of view, the high point of closed teeth fully utilized the deformation of the spring, while the low point of closed teeth did not exert the maximum potential of the spring. However, the high point of the closed cam must be full, while the low point is not needed. Therefore, when closing teeth with a high point, it is necessary to consider its importance. In general, the closed teeth of the impression cylinder should be closed with high points, and the middle transfer cylinder can be closed with low points.
8. Requirements of the drum
The roller is the most used part of the printing unit, and it is inextricably linked to the quality of the printed product, so its requirements are also more demanding.
(1) Utilization rate of the roller The utilization rate of the roller is the ratio of the arc length of the non-notch portion of the roller to the circumference of the roller (between 0-1). The larger this ratio is, the higher the utilization rate of the roller is. Therefore, the large drum surface must be the main direction for the development of rotary offset presses.
(2) Diameter of the roller The smaller the diameter of the roller, the better. The smaller the diameter, the easier the machining accuracy can be guaranteed. However, due to the limitations of the printing format, it is impossible to go infinitely small.
(3) The length of the drum The shorter the drum, the better. The shorter the rigidity is, the better the pressure is. Therefore, the product of the four boot printing should be printed better under the same conditions.
(4) Balance of the roller The balance of the roller directly affects the stability of the operation, so it is best to perform a dynamic balance test on the roller.
(5) The accuracy of the drum surface The higher the precision of the drum surface, the higher the quality of the printed product, so the surface of the drum must generally be ground.
(6) Drum surface material Due to the relatively large amount of acidic materials in the printing environment, the surface of the drum is easily rusted, so the surface must be resistant to corrosion. In addition, the surface of the roller must also have high strength and hardness in order to ensure the quality of the print and resist fatigue shock.
(7) The weight of the drum The greater the weight of the drum, the greater the rotational inertia and the more difficult it is to brake. Therefore, we must fully consider this point when designing a new drum. Under the premise of ensuring the strength, the lighter the better.
Geneva Watch Series Co., Ltd. , http://www.nsdigitalwatch.com