4.4 There is no adhesion between upper and lower sheets
Due to friction on the surface of the paper during printing, static electricity is generated. To eliminate static electricity, in addition to ensuring proper temperature and humidity, another is to install a dedicated static elimination device at the delivery. The adhesion of ink between printed sheets must be avoided during the delivery process. The main method of preventing stickiness is dusting, and by dusting, the back surface of the upper sheet and the front surface of the lower sheet are brought into contact with each other. The dusting and drying of the ink are mutually shielded. The amount of dusting must be taken into account. Of course, there are other factors that need to be considered. The following brief analysis of these matters needing attention.
1. The thinner the powder, the better. It is best to keep it from becoming dirty until it has a minimal effect on drying.
2. The powder should not be too fine. Too thin, the stronger the hiding power of the surface of the printed product, the slower the drying of the ink.
3. The powder can not be too thick. The coarser it is, the worse the homogeneity is, where the powdered particles are separated upwards and downwards, and where there are no particles, the upper and lower papers may stick together.
4. The most effective use of powder. A control device for the dusting area is provided at the delivery portion, and even if it is sprayed on the effective printing surface, the non-printing portion is not sprayed. The length of time of spraying can be adjusted steplessly according to the paper web (this adjusting device is generally installed on the sprocket above the delivery pile). The right and left dusting position adjustment can control the spraying of each nozzle separately, as shown in Figure 4.6 As shown.
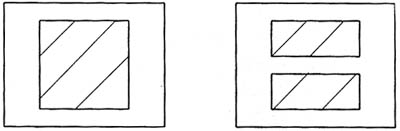
5. Impact on human health. Although powder is non-toxic, it is not good if it flies into people's eyes or nostrils. Therefore, the farther possible from the operator is, the better the position of dusting is. Some machine dusting devices are installed near the delivery roller, and some machines are installed near the brake roller. The former is relatively far from people, and it has the least impact on people in the shroud of the delivery part, but it is dusted after it is printed, which is disadvantageous to the drying of the ink. The latter is closer to people and it is very easy to fly to people. It has a great impact on people, but it only begins to spray when the printed sheets fall on the paper stack, and has the least influence on the drying of the ink.
6. The impact on the equipment. Due to the presence of air flow, the particles may fly to the chains on either side, or other relative operating locations. After the powder falls to the top, the mutual friction between the contact surfaces is increased, resulting in wear and damage to the contact accuracy and the stability of operation. Therefore, from this point of view, the particles should be prevented from leaving the print surface as much as possible.
7. The effect on the quality of the equipment and the printed product when turning over. When the printing is reversed, the particles on the print may float to various parts of the machine, which has a greater impact on the equipment. At the same time, the powder on the surface of the print will be transferred to the blanket to affect the transfer of the ink, and the quality of the print cannot be guaranteed.
8. In the field, the amount of powder sprayed is large; at the flat screen, the amount of powder sprayed is small.
9. Strictly control the amount of powder when coloring, and relax when not coloring. If the amount of powder is not strictly controlled during color registration, there may be too much powder during printing, and the subsequent ink cannot be transferred to the surface of the printed product.
To sum up, the principle of controlling the amount of powder to be sprayed is: within the effective part of the printing, the upper and lower printed sheets do not adhere to each other. At this time, the amount of powder used is the best amount of powder.
The purpose of dusting is to prevent contact between the upper and lower print sheets. The main reason is that the ink on the surface of the prints is not completely dry. If the ink is dry, dusting has no meaning. Therefore, some existing equipment has been equipped with a drying device to accelerate the drying of the ink, which can reduce or even do not spray. However, when the paper is damped and then heated, the surface of the paper may be easily deformed. Once it is deformed, it is often impossible to recover, which has a great influence on the color registration. Therefore, it must be used with caution. In theory, powder spraying is required in the graphic and text areas, and no painting is required in places without graphics. However, this control is difficult, but people are working hard in this direction.
Double Pipe Making Machine,Upvc Water Pipe Machine,Plastic Pipe Making Machine,Pvc Pipe Machine
Ruijie Plastic Machinery Co., Ltd. , http://www.vulcanizingpress.com