4 Take-up section
The take-up part is the last printing unit of the printing press. Its main function is to stack the printed sheets together. However, this stacking is not carried out arbitrarily, and it has strict requirements: 1 The surface of the printed sheet is flat; 2 The front sheet of the printed sheet is flush; 3 The side sheet of the printed sheet is flush; 4 The upper and lower sheets are not bonded together. ;5 Printed surface can not have any scratches.
The above-mentioned five points are called the free state of the paper at the delivery place. In the printing process, the paper is actually a process from the free state to the controlled state and back to the free state.
1. The printed surface is flat. This is one of the most basic requirements for printed products. The pleats on the surface of the printed product have a certain influence on the quality of the printed product. The uneven surface brings difficulties to the subsequent processing of the prints, so the surface must be flat.
2. The front flap of the printed sheet is flush. The front flap of the printed sheet is flush and easy to check or cut. It is also conducive to the stacking of printed sheets at the delivery pile.
3. The side of the printed sheet is flush. The reason is the same as 2.
4. There is no adhesion between the upper and lower sheets. If the upper and lower sheets are stuck together, the image on the surface of the printed product will be damaged, and the subsequent process will cause great trouble.
5. The printed surface must not have any scratches. If scratches appear on the surface of the print, the quality of the print will be affected. In severe cases, it can only be considered as a waste product.
The basic composition of the delivery section can be analyzed based on the requirements for the state of the sheet at the delivery location.
4.1 Surface Leveling of Sheets (Leveler)
The sheet reaches the delivery section from the printing unit, and the trailing edge of the sheet undergoes bending deformation. If there is no flattening device in the middle, its flatness cannot be guaranteed, as shown in Figure 4.1.
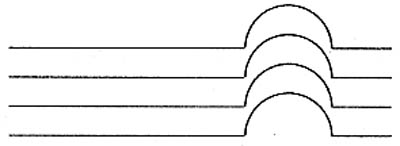
As the print sheets rotate with the impression cylinder, they remain stationary with each other (regardless of the speed difference between the blanket cylinder and the impression cylinder). When the impression cylinder handed the paper over to the delivery roller, there is a certain amount of shrinkage due to the delivery roller, that is, after passing the point of intersection, the linear velocity of the tooth pad is lower than the linear velocity of the tooth pad on the surface of the drum. The speed of the paper suddenly dropped. The second half of the printed sheet is not separated from the blanket cylinder in time, but it is rotated along with the blanket cylinder until the printed sheet is again in the tensioned state, and the printed sheet begins to separate synchronously. In the process of separation from splicing to synchronism, the printed sheet is in a state of being relaxed to a sudden tension, and a fold is formed near the surface of the blanket. If this offset is not eliminated, it will affect the flatness of the printed sheet. Figure 4.2 shows the entire forming process of the seal.
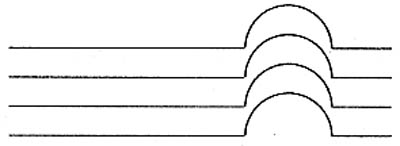
Therefore, the printer of this structure is generally equipped with a sheet leveling device (also called an anti-roll device) at the delivery portion. The role of the press leveling device (leveler) is to level the second half of the printed sheet. The working principle is shown in Figure 4.3.
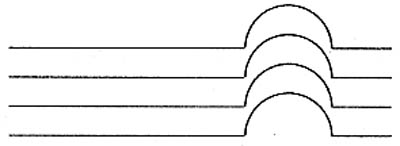
An air suction device is installed between the two rollers to form a pressure difference after suction, and the pressure of the air corrects the bent position of the printed sheet.
The most thorough way to eliminate the curl of the printed sheets is to eliminate the conditions for their existence, which needs to be solved from the design. There are two methods currently used:
1 The printed sheet is completely printed on the impression cylinder and then delivered to the delivery roller. This method generally uses a double-diameter impression cylinder.
2 Two additional transfer cylinders are added behind the impression cylinder so that the print sheet completely separates from the blanket cylinder after passing through the two transfer cylinders. There is no process from tensioning to relaxation and then tensioning. Figure 4.4 shows.
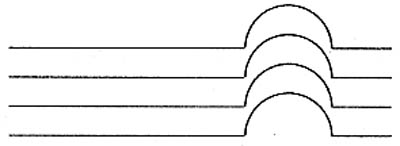
If the above method is used, the leveling device can be removed.
Geneva Watch Series Co., Ltd. , http://www.nsdigitalwatch.com